What Is a Machine Vision Camera?
A machine vision camera, also known as an industrial camera, is a key part of a 2D image processing system. Its main function is to capture images, which are then processed by a combination of hardware and software. The information obtained is prepared for various applications.
A typical example of an image processing application in a manufacturing system is quality control, presence control and completeness control. This involves analyzing a specific feature of a part that is produced on an assembly line. In this way, it can be checked whether the part meets the quality criteria or, if necessary, must be sorted out.

Main Components of 2D Image Processing Systems
The Difference Between Machine Vision Cameras and Smart Cameras
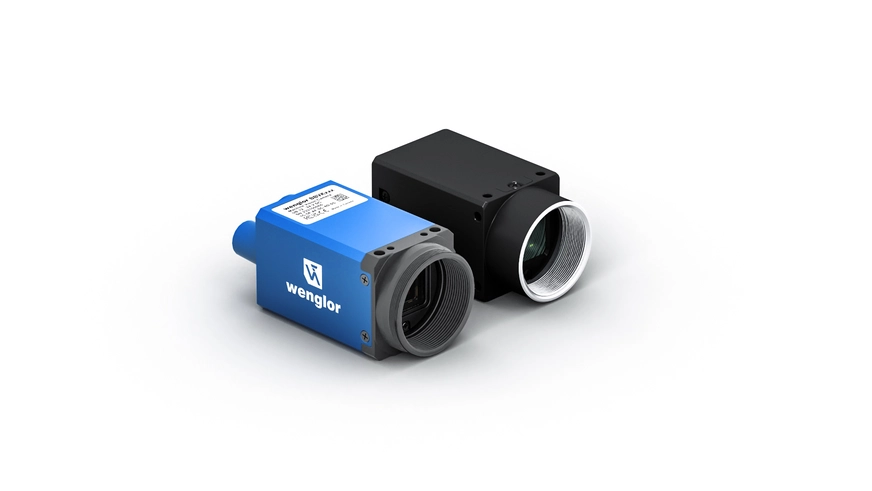
Machine Vision Cameras
Image evaluation takes place via the machine vision controller and the image processing software
Multiple cameras can be connected to a single machine vision controller
Faster process times thanks to high computing power of the machine vision controller
Suitable for very high resolution inspection tasks
Compact camera design
Applications of Machine Vision Cameras
Position Check
Robot Positioning
Parts Measurement
Quality Control
Presence Check
Process Monitoring
Code Reading
Reliable Solution for Cross-Industry Applications

Automotive Industry
Quality inspection of car interior doors
Quality inspection of engine blocks
Position detection for automated tightening

Electronics Industry
Position check of PCBs
Checking the alignment of components
Inspection of plug connectors and cables

Packaging Industry
Check packages for damage, contamination or missing labels
Label inspection of packaging
Minimum shelf life test on PET bottles

Food Industry
Orientation of beverage cans
Label check on packaging
Tethered cap inspection
This Is the Difference Between Surface and Line Cameras

Line Cameras
Image capture takes place line by line (movement is necessary to capture the object) |
Image quality dependent on motion and time of image capture |
Ideal for applications with moving objects and endless materials |
High speed |
Operating Orinciple of CMOS Sensors with Global or Rolling Shutter
CMOS image sensors have two exposure methods that control how an image is captured and read. These procedures determine the exposure time and thus the amount of light that is converted into electrons as a value in the camera sensor. A distinction is made between global shutter and rolling shutter:

Global Shutter
Entire image area is exposed simultaneously |
Suitable for static as well as dynamic applications |
No image distortion on moving objects |

Rolling Shutter
Lines are exposed with a time offset |
For static applications |
Image distortions due to fast object movements (rolling shutter effect) |
Capturing still images |

The Rolling Shutter Effect
Monochrome or Color Camera? Which Do I Use When?
Actual Image

使用单色相机拍摄图像

单色相机能够将物体与背景区分开来。
使用彩色相机拍摄图像

彩色相机能够将物体彼此区分开来,并与背景区分开来。
在工业图像处理中,需要区分单色相机和彩色相机。单色相机可捕捉灰度,并聚焦于图像中的亮度差异。因此它们特别适用于需要精细对比度和细节的应用,例如表面检测或物体测量。
相反,彩色相机可以捕捉颜色信息,使其能够更精确地捕捉表面。它们可以分析整个色谱,并由此提供更详细、更多样化的图像再现。这使其非常适合颜色发挥重要作用的应用场景,例如产品质量控制,其中颜色差异可能表明材料存在缺陷。
安装机器视觉照相机时的注意事项
机器视觉照相机的接口
千兆以太网 (GigE)

Fast transfer of large amounts of image data
Easy integration thanks to protocol standard
- Multiple cameras can be operated in a network
It is also possible to connect the machine vision camera via a cable using PoE (Power over Ethernet), which means that both power supply and data transfer take place via a single connection.
分辨率
帧频
曝光时间
为每种应用提供适当的分辨率
分辨率 | 精度 | 例如 |
---|---|---|
1.6 MP | 不需要极高分辨率的应用 | 光学字符识别、装配检查、存在性检查 |
5 MP | 需要中等细节精度的应用 | 检查包装 |
12 MP | 需要高精度的应用 | 精细机械部件的检测 |
24 MP | 需要极高分辨率和细节精度的应用 | 检查印刷线路板元件是否有缺陷 |