Outstanding Performance and Efficiency: The weCat3D Series for Welding Systems
After the welding process has been completed, the result must be checked. Irregularities such as missing, double, undulated or other faulty welds are reliably detected by 2D/3D profile sensors and output via the defined interface. A common automatic test method is visual inspection. The use of a profile sensor offers decisive advantages in this procedure: the time required for checking and analyzing the welding seams is reduced without compromising on the quality of the inspection.
- Precise checking along the welding seam
- Excellent profile quality – even on reflective surfaces
- Compact housing (IP67)
- Easy sensor integration thanks to existing SDKs and the standard Ethernet TCP/IP interface
- High profile density for the smallest error detection with Z resolution from 2 μm
- Material and color independent
- High measurement frequency
How the Weld Seam Inspection Works
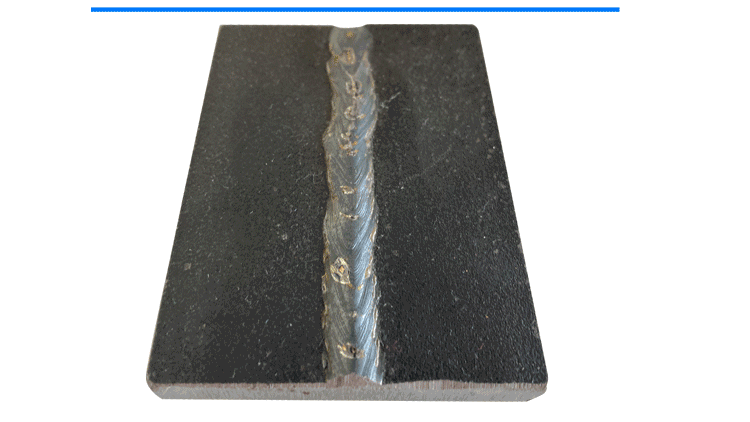
During the visual weld seam inspection, the profile sensor is guided along the real welding seam. The sensor is positioned so that the profile line generated is perpendicular to the welding seam. The joining of the individual profiles in the application software creates a 3D image, which is examined by the software for irregularities – taking into account a set tolerance. If deviations are found during the subsequent evaluation, a corresponding signal is output by the software.
Versatile for Welding Processes

With the following types of welding, for example:
- MIG – Metal Inert Gas
Metal welding with inert, i.e. inactive gases
- MAG – Metal Active Gas
Metal welding with active gases
- WIG – Wolfram Inert Gas
Metal welding with a non-melting pure or alloy tungsten electrode
- Laser welding (EN ISO 4063: Process 52)
Laser welding permits high welding speeds with highly precise results
Irregularities After Applying the Welding Seam
No seam

Hole

Missing edge formation

Pore

Protrusion

Curvature

Seam angle

Seam angle

Welding seam position

Root sag

Clearance

Root concavity

A-dimension

A-dimension camber

Dipping

Arching

Seam burr

Edge height

Practical Examples and Collaborations
The versatility of wenglor’s innovative sensor is underlined by its use in various industries. In combination with the robot cell and the integrator’s software, the desired welding result is ensured, which minimizes follow-up costs and maximizes product safety, for example. This is why they are used in numerous industries:
|
|
|
|
|
|